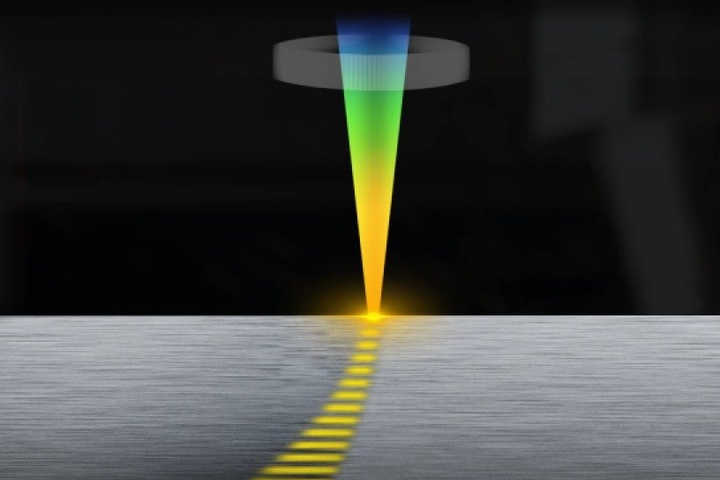
HOW TO IMPROVE PRODUCTION EFFICIENCY OF A LASER PLATE CUTTING MACHINE
How to Improve Production Efficiency of a Laser Plate Cutting Machine
Laser plate cutting machines are invaluable tools in the manufacturing industry, offering precision and speed for cutting metal plates and other materials. However, just having a laser plate cutting machine isn’t enough to guarantee maximum efficiency. Proper setup, routine maintenance, operator training, and strategic use of technology are all crucial to enhancing productivity, reducing costs, and ultimately maximizing output. In this post, we’ll explore various methods to improve the efficiency of a laser plate cutting machine and ensure it meets production goals effectively.
1. Optimize Material Usage and Cutting Path
One of the primary factors impacting the efficiency of a laser plate cutting machine is material handling and usage. Effective material management reduces waste and shortens production time, directly improving productivity.
Nesting Software: Using advanced nesting software can optimize material layout, reducing the amount of scrap material produced. By efficiently arranging parts on a sheet, manufacturers can maximize each plate’s usable surface area and minimize waste.
Path Optimization: Optimizing the cutting path can drastically cut down production time. For example, grouping cuts based on their position on the plate reduces the time spent moving the cutting head back and forth across the material.
Laser Power and Speed Settings: Adjusting power and speed settings based on material type can also enhance efficiency. For thin materials, higher cutting speeds with optimized power can increase throughput, while thicker materials may require slower speeds and more power.
2. Routine Maintenance to Prevent Downtime
The condition of a laser plate cutting machine directly affects its efficiency. Regular maintenance ensures the machine operates at its best and reduces the risk of unexpected breakdowns, which can halt production entirely.
Lens and Mirror Cleaning: The optics of a laser cutting machine, particularly lenses and mirrors, can quickly become dirty. Contaminants on the lenses and mirrors reduce laser power and, consequently, cutting efficiency. Regular cleaning keeps the laser beam focused and ensures a smooth, clean cut.
Lubrication: Moving parts, such as guide rails and bearings, need to be regularly lubricated to reduce friction and ensure smooth operation. Well-lubricated parts experience less wear, reducing the need for repairs and replacements.
Filter Replacement: Most laser plate cutting machines come with filters that prevent debris from contaminating the machine’s internal components. Changing these filters on a scheduled basis ensures the machine’s parts are protected and its operation remains efficient.
A well-maintained machine experiences fewer failures, reducing costly downtime and increasing overall production efficiency. In addition, if you’re in the market for a reliable laser plate cutting machine supplier, ask about their support and maintenance services, as these can be valuable for long-term efficiency.
3. Invest in Training and Skilled Operators
A laser plate cutting machine is only as effective as the person operating it. Even with the most advanced machine, an inexperienced or untrained operator can slow down production and lead to mistakes.
Comprehensive Training: Investing in thorough training for operators on machine functions, maintenance routines, and safety measures pays off in the long run. Knowledgeable operators understand how to adjust settings, interpret data, and quickly resolve minor issues that might otherwise cause delays.
Regular Skill Updates: As machines and software evolve, ensuring that operators receive updated training keeps them efficient and reduces the chances of costly errors. Operators familiar with the latest features and techniques can maximize machine capabilities.
Additionally, experienced operators know how to balance machine speed with cut quality, ensuring each part meets standards without excessive time spent fine-tuning.
4. Leverage Automation for Higher Throughput
Automation can significantly increase the efficiency of a laser plate cutting machine by handling routine tasks, freeing up operators to focus on more strategic work, and reducing the risk of human error.
Automated Loading and Unloading Systems: Automating the process of loading and unloading plates can streamline production and reduce idle time between jobs. These systems ensure the machine is always running, maximizing productivity.
Real-Time Monitoring and Data Analytics: With modern software solutions, operators and managers can monitor the machine’s performance in real-time. Data analytics can reveal patterns in productivity, allowing managers to adjust workflows for maximum efficiency.
Integration with ERP Systems: Integrating the laser cutting machine’s software with the company’s ERP system allows for seamless inventory management, scheduling, and tracking, further enhancing production efficiency.
Automation may come with an initial investment, but it’s often worthwhile. A laser plate cutting machine with automated features may have a higher upfront laser plate cutting machine price, but it quickly pays off through increased output and reduced labor costs.
5. Choose the Right Machine for Your Needs
When selecting a laser plate cutting machine, it’s essential to choose one that fits your production requirements. For example, some machines are better suited for high-volume production, while others are optimized for precision cuts on smaller batches.
Power and Speed Capabilities: Higher wattage machines cut through thicker materials faster, which can be beneficial if you frequently work with heavy plates. However, if your business primarily handles thin sheets, a lower-wattage, high-speed machine may be more efficient.
Table Size and Loading Capacity: The size of the cutting table and the machine’s material capacity also impact efficiency. Larger tables allow for more extensive cutting layouts and reduce the frequency of reloading material, while higher loading capacities support continuous production.
If you’re working with a laser plate cutting machine supplier, discuss your specific needs with them to find the right machine for your business. A well-suited machine will optimize production and reduce energy and maintenance costs over time.
6. Analyze Workflow and Improve Production Scheduling
Production scheduling and workflow are crucial elements in ensuring a laser cutting operation runs smoothly. By evaluating and optimizing the workflow, managers can minimize bottlenecks and keep machines running at optimal capacity.
Prioritize Orders Based on Machine Capabilities: Organize cutting jobs by material type and thickness to minimize setup changes. Scheduling similar jobs together reduces downtime and ensures operators make fewer adjustments between tasks.
Evaluate Time Spent on Non-Value-Added Tasks: Identify any non-essential steps in the production process that add to the overall lead time. By eliminating these, production runs faster, and the laser plate cutting machine spends more time cutting, not waiting.
Monitor for Bottlenecks and Adjust: Using real-time data from automated tracking systems, managers can identify production bottlenecks and adjust processes or add shifts to keep production moving efficiently.